山東埃爾派 | 點(diǎn)擊量:0次 | 2020-11-14
SMT回流焊接產(chǎn)生“錫珠”的原因分析及防控措施
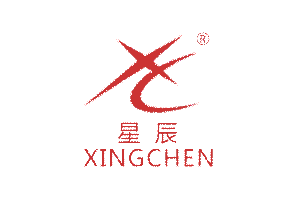
“SMT表面貼裝”制程“錫珠”出現(xiàn)的原因及預(yù)防控制辦法
在“SMT表面貼裝”焊接制程中,回流焊的“溫度、時(shí)間、焊膏的質(zhì)量、印刷厚度、鋼網(wǎng)(模板)的制作、裝貼壓力”等因素都有可能造成“錫珠”的產(chǎn)生。因此,找到“錫珠”可能出現(xiàn)的原因,并加以預(yù)防與控制就是達(dá)成板面無“錫珠”的關(guān)鍵之所在。
(一),焊膏本身質(zhì)量原因可能引起的“錫珠”狀況
1,焊膏中的金屬含量。焊膏中金屬含量的質(zhì)量比約為89-91%,體積比約為50%左右。通常金屬含量越多,焊膏中的金屬粉末排列越緊密,錫粉的顆料之間有更多機(jī)會結(jié)合而不易在氣化時(shí)被吹散,因此不易形成“錫珠”;如果金屬含量減少,則出現(xiàn)“錫珠”的機(jī)率增高。
2,焊膏中氧化物的含量。焊膏中氧化物含量也影響著焊接效果,氧化物含量越高,金屬粉末熔化后在與焊盤熔合的過程中表面張力就越大,而且在“回流焊接段”,金屬粉末表面氧化物的含量還會增高,這就不利于熔融焊料的完全“潤濕”從而導(dǎo)致細(xì)小錫珠產(chǎn)生。
3,焊膏中金屬粉末的粒度。焊膏中的金屬粉末是極細(xì)小的近圓型球體,常用的焊粉球徑約在25-45μm之間,較細(xì)的粉末中氧化物含量較低,因而會使“錫珠”現(xiàn)象得到緩解。
4,焊膏抗熱坍塌效果。在回流焊預(yù)熱段,如果焊膏抗熱坍塌效果不好,在焊接溫度前(焊料開始熔融前)已印刷成型的焊膏開始坍塌,并有些焊膏流到焊盤以外,當(dāng)進(jìn)入焊接區(qū)時(shí),焊料開始熔融,因?yàn)閮?nèi)應(yīng)力的作用,焊膏收縮成焊點(diǎn)并開始浸潤爬升至焊接端頭,有時(shí)因?yàn)楹竸┤笔Щ蚱渌驅(qū)е潞父鄳?yīng)力不足,有一少部分焊盤外的焊膏沒有收縮回來,當(dāng)其完全熔化后就形成了“錫珠”。
由此可見,焊膏的質(zhì)量及選用也影響著錫珠產(chǎn)生,焊膏中金屬及其氧化物的含量,金屬粉末的粒度、焊膏抗熱坍塌效果等都在不同程度地影響著“錫珠”的形成。
(二),使用不當(dāng)形成 “錫珠”的原因分析
1,“錫珠”在通過回流焊爐時(shí)產(chǎn)生的。我們大致可以將回流焊過程分為“預(yù)熱、保溫、焊接和冷卻”四個(gè)階段。“預(yù)熱段”是為了使印 制板和表貼元件緩慢升溫到120-150℃之間,這樣可以除去焊錫膏中易揮發(fā)的溶劑,減少對元件的熱沖擊。而在這一過程中焊膏內(nèi)部會發(fā)生氣化現(xiàn)象,這時(shí)如果焊膏中金屬粉末之間的粘結(jié)力小于焊劑氣化產(chǎn)生的力,就會有少量“焊粉”從焊盤上流下或飛出,在“焊接”階段,這部分“焊粉”也會熔化,從而形成“錫珠”。由此可以得出這樣的結(jié)論“預(yù)熱溫度越高,預(yù)熱速度越快,就會加劇焊劑的氣化現(xiàn)象從而引起坍塌或飛濺,形成錫珠”。因此,我們可以采取較適中的預(yù)熱溫度和預(yù)熱速度來控制“錫珠”的形成。
2,焊膏在印制板上的印刷厚度及印刷量。焊膏的印刷厚度是生產(chǎn)中一個(gè)主要參數(shù),印刷厚度通常在0.15-0.20mm之間,過厚或過多就容易導(dǎo)致“坍塌”從而形成“錫珠”。在制作鋼網(wǎng)(模板)時(shí),焊盤的大小決定著模板開孔的大小,通常,我們?yōu)榱吮苊夂父嘤∷⑦^量,將印刷孔的尺寸控制在約小于相應(yīng)焊盤接觸面積10%,結(jié)果表明這樣會使“錫珠”現(xiàn)象有一定程度的減輕。
3,如果在貼片過程中貼裝壓力過大,當(dāng)元件壓在焊膏上時(shí),就可能有一部分焊膏被擠在元件下面或有少量錫粉飛出去,在焊接段這部分焊粉熔化從而形成“錫珠”;因此,在貼裝時(shí)應(yīng)選擇適當(dāng)?shù)馁N裝壓力。
4,焊膏通常需要冷藏,在使用前一定要使其恢復(fù)至室溫方可打開包裝使用,如果焊膏溫度過低就被打開包裝,會使膏體表面產(chǎn)生水分,這些水分在經(jīng)過預(yù)熱時(shí)會造成焊粉飛出,在焊接段會讓熱熔的焊料飛濺從而形成“錫珠”。
我國一般地區(qū)夏天的空氣濕度較大,把焊膏從冷藏取出時(shí),一般要在室溫下回溫4-5小時(shí)再開啟瓶蓋。
5,生產(chǎn)或工作環(huán)境也影響“錫珠”的形成,當(dāng)印制板在潮濕的庫房存放過久,在裝印制板的包裝袋中發(fā)現(xiàn)細(xì)小的水珠,這些水分和焊膏吸潮的水分一樣,會影響焊接效果從而形成“錫珠”。因此,如果有條件,在貼裝前將印制板或元器件進(jìn)行一定的烘干,然后進(jìn)行印刷及焊接,能夠有效地抑制“錫珠”的形成。
6,焊膏與空氣接觸的時(shí)間越短越好,這也是使用焊膏的一個(gè)原則。取出一部分焊膏后,立即蓋好蓋子,特別是里面的蓋子一定要向下壓緊,將蓋子與焊膏之間空氣擠出,否則對焊膏的壽命會有一定的影響,同時(shí)會造成焊膏的干燥加快或在下次再使用時(shí)吸潮,從而形成“錫珠”。
由此可見,“錫珠”的出現(xiàn)有很多原因,只從某一個(gè)方面進(jìn)行預(yù)防與控制是遠(yuǎn)遠(yuǎn)不夠的。我們需要在生產(chǎn)過程中研究如何防制各種不利因素及潛在隱患,從而使焊接達(dá)到最好的效果,避免“錫珠”的產(chǎn)生。
(三),“SMT表面貼裝”過程的“錫珠”預(yù)防與控制
1,焊膏的選用
在選擇焊膏時(shí),應(yīng)堅(jiān)持在現(xiàn)有工藝條件下的試用,這樣,既能驗(yàn)證供應(yīng)商焊膏對自身產(chǎn)品、工藝的適用性,也能初步了解該焊膏在實(shí)際使用中的具體表現(xiàn)。對焊膏方面的評估,應(yīng)注意各種常見的參數(shù),比如“焊油與焊粉的比例、錫球的顆粒度”等。
正確選擇的焊膏不一定是各項(xiàng)參數(shù)都最優(yōu)異,更多的情況下,對于SMT的工藝制程及產(chǎn)品特性來講,適合的就是最好的。因此,選擇適合自身工藝及產(chǎn)品的焊膏,并將所有參數(shù)定下來,在以后的供應(yīng)商交貨過程中做出品管驗(yàn)收及品檢的依據(jù),一方面核對供應(yīng)商所提供的書面資料,另一方面取少量不同批次的產(chǎn)品進(jìn)行試用。
優(yōu)質(zhì)供應(yīng)商,會在配合過程中提出相應(yīng)的工藝建議,并根據(jù)客戶具體要求進(jìn)行焊膏產(chǎn)品的升級及缺陷改進(jìn);因此,相對穩(wěn)定的、誠信度高的供應(yīng)商,對客戶在焊膏質(zhì)量方面預(yù)防及控制“錫珠”能提供很大的幫助。
2,“SMT表面貼裝”工藝控制與改進(jìn)
在所有的工藝控制過程中,從焊膏的保存及取出使用、回溫、攪拌都有嚴(yán)格的文件規(guī)定,主要有以下幾個(gè)方面的重點(diǎn):
(1),嚴(yán)格按照供應(yīng)商提供的存貯條件及溫度進(jìn)行存貯,一般情況下焊膏應(yīng)存貯于0-10℃的冷藏條件下;
(2),焊膏取出后、使用前,應(yīng)該進(jìn)行常溫下的回溫,在焊膏未完全回溫前,不得開啟;
(3),在攪拌過程中,應(yīng)該按照供應(yīng)商所提供的攪拌方法及攪拌時(shí)間進(jìn)行攪拌;
(4),在印刷過種中,應(yīng)該注意印刷的力度,及鋼網(wǎng)表面的清潔度,及時(shí)擦拭鋼網(wǎng)表面多余的焊膏殘留,防止在這個(gè)過程污染PCB板面從而造成焊接過程中的錫珠產(chǎn)生。
(5),回流焊過程中,應(yīng)嚴(yán)格按照已經(jīng)訂好的回流焊曲線進(jìn)行作業(yè),不得隨意調(diào)整;同時(shí)應(yīng)該經(jīng)常校驗(yàn)回流焊曲線與標(biāo)準(zhǔn)曲線的差異并修正;
(6),在“SMT表面貼裝”工藝中,鋼網(wǎng)(模板)的“開口方式”以及“開口率”很可能導(dǎo)致焊膏在“印刷特性”及“焊接特性”方面的一些缺陷從而引起“錫珠”。在相關(guān)實(shí)驗(yàn)中,我們對鋼網(wǎng)進(jìn)行了改進(jìn),將原來易產(chǎn)生“錫珠”的片式元件1:1鋼網(wǎng)開口,改為1:0.75的楔形,改后試驗(yàn)效果較好“錫珠”產(chǎn)生的機(jī)率明顯下降直至基本杜絕。
通過修改鋼網(wǎng)的開口方式和批量的印刷試驗(yàn),可以很明顯地看到,改后鋼網(wǎng)的開口方法可以有效防控“錫珠”的產(chǎn)生。修改后“防錫珠”鋼網(wǎng)的印刷效果及焊接效果
按照多次的對比實(shí)驗(yàn),并結(jié)合“圖二”可以看出,通過修改前后三次的效果對比,第二次修改后的鋼網(wǎng),沒有見到明顯的錫珠,而錫膏的焊錫量也沒有偏少。由此說明通過鋼網(wǎng)的開口改變,對“SMT表面貼裝”制程中的“錫珠”防控還是有一定效果的。同時(shí)我們對更改后的焊接產(chǎn)品送到“賽寶實(shí)驗(yàn)室”進(jìn)行檢測(報(bào)告編號為“FX03-2081691”),通對該線路板上的0603元件進(jìn)行推剪力測試,在“R124、R125、R126、C16、C57”五個(gè)元件點(diǎn)的剪切力分別為“58.14N、56.53N、51.87N、50.90N、52.35N”,焊接強(qiáng)度能達(dá)到我們的要求。
“SMT表面貼裝”制程雖然對“錫珠”的防控較為復(fù)雜,但經(jīng)過長期的工作努力及經(jīng)驗(yàn)積累,相信可以做到無“錫珠”,或有效降低“錫珠”產(chǎn)生的機(jī)率。
三,“波峰焊”過程中出現(xiàn)“錫珠”的原因及預(yù)防控制辦法
在“波峰焊”工藝過程中,“錫珠”的產(chǎn)生有兩種狀況:一種是在板子剛接觸到錫液時(shí),因?yàn)橹竸┗虬宀谋旧淼乃葸^多或高沸點(diǎn)溶劑沒有充分揮發(fā),遇到溫度較高的錫液時(shí)驟然揮發(fā),較大的溫差致使液態(tài)焊錫飛濺出去,形成細(xì)小錫珠;另一種情況是在線路板離開液態(tài)焊錫的時(shí)候,當(dāng)線路板與錫波分離時(shí),線路板順著管腳延伸的方向會拉出錫柱,在助焊劑的潤濕作用及錫液自身流動性的作用下,多余的焊錫會落回錫缸中,因此而濺起的焊錫有時(shí)會落在線路板上,從而形成“錫珠”。
因此,我們可以看到,在“波峰焊”防控“錫珠”方面,我們應(yīng)該從兩個(gè)大的方面著手,一方面是助焊劑等原材料的選擇,另一方面是波峰焊的工藝控制。
(一),助焊劑方面的原因分析及預(yù)防控制辦法
1、助焊劑中的水份含量較大或超標(biāo),在經(jīng)過預(yù)熱時(shí)未能充分揮發(fā);
2、助焊劑中有高沸點(diǎn)物質(zhì)或不易揮發(fā)物,經(jīng)預(yù)熱時(shí)不能充分揮發(fā);
這兩種原因是助焊劑本身“質(zhì)量”問題所引起的,在實(shí)際焊接工藝中,可以通過“提高預(yù)熱溫度或放慢走板速度等來解決”。除此之外,在選用助焊劑前應(yīng)針對供商所提供樣品進(jìn)行實(shí)際工藝的確認(rèn),并記錄試用時(shí)的標(biāo)準(zhǔn)工藝,在沒有“錫珠”出現(xiàn)的情況下,審核供應(yīng)商所提供的其他說明資料,在以后的收貨及驗(yàn)收過程中,應(yīng)核對供應(yīng)商最初的說明資料。
(二),工藝方面的原因分析及預(yù)防控制辦法
1,預(yù)熱溫度偏低,助焊劑中溶劑部分未完全揮發(fā);
2,走板速度太快未達(dá)到預(yù)熱效果;
3,鏈條(或PCB板面)傾角過小,錫液與焊接面接觸時(shí)中間有氣泡,氣泡爆裂后產(chǎn)生錫珠;
4,助焊劑涂布的量太大,多余助焊劑未能完全流走或風(fēng)刀沒有將多余焊劑吹下;
這四種不良原因的出現(xiàn),都和標(biāo)準(zhǔn)化工藝的確定有關(guān),在實(shí)際生產(chǎn)過程中,應(yīng)該嚴(yán)格按照已經(jīng)訂好的作業(yè)指導(dǎo)文件進(jìn)行各項(xiàng)參數(shù)的校正,對已經(jīng)設(shè)定好的參數(shù),不能隨意改動,相關(guān)參數(shù)及所涉及技術(shù)層面主要有以下幾點(diǎn):
(1),關(guān)于預(yù)熱:一般設(shè)定在90℃-110℃,這里所講“溫度”是指預(yù)熱后PCB板焊接面的實(shí)際受熱溫度,而不是“表顯”溫度;如果預(yù)熱溫度達(dá)不到要求,則焊后易產(chǎn)生錫珠。
(2),關(guān)于走板速度:一般情況下,建議客戶把走板速度定在1.1-1.4米/分鐘,但這不是絕對值;如果要改變走板速度,通常都應(yīng)以改變預(yù)熱溫度作配合;比如:要將走板速度加快,那么為了保證PCB焊接面的預(yù)熱溫度能夠達(dá)到預(yù)定值,就應(yīng)當(dāng)把預(yù)熱溫度適當(dāng)提高;如果預(yù)熱溫度不變,走板速度過快時(shí),焊劑有可能揮發(fā)不完全,從而在焊接時(shí)產(chǎn)生“錫珠”。
(3),關(guān)于鏈條(或PCB板面)的傾角:這一傾角指的是鏈條(或PCB板面)與錫液平面的角度,當(dāng)PCB板走過錫液平面時(shí),應(yīng)保證PCB零件面與錫液平面只有一個(gè)切點(diǎn);而不能有一個(gè)較大的接觸面;當(dāng)沒有傾角或傾角過小時(shí),易造成錫液與焊接面接觸時(shí)中間有氣泡,氣泡爆裂后產(chǎn)生“錫珠”。
(4),在波峰爐使用中,“風(fēng)刀”的主要作用是吹去PCB板面多余的助焊劑,并使助焊劑在PCB零件面均勻涂布;一般情況下,風(fēng)刀的傾角應(yīng)在10度左右;如果“風(fēng)刀”角度調(diào)整的不合理,會造成PCB表面焊劑過多,或涂布不均勻,不但在過預(yù)熱區(qū)時(shí)易滴在發(fā)熱管上,影響發(fā)熱管的壽命,而且在浸入錫液時(shí)易造成“炸錫”現(xiàn)象,并因此產(chǎn)生“錫珠”。
在實(shí)際生產(chǎn)中,結(jié)合自身波峰焊的實(shí)際狀況,對相關(guān)材料進(jìn)行選型,同時(shí)制訂嚴(yán)格《波峰焊操作規(guī)程》,并嚴(yán)格按照相關(guān)規(guī)程進(jìn)行生產(chǎn)。經(jīng)過實(shí)驗(yàn)證明,在嚴(yán)格落實(shí)工藝技術(shù)的條件下,完全可以克服因?yàn)?ldquo;波峰焊焊接工藝問題”產(chǎn)生的“錫珠”。
四,“手工焊”過程中“錫珠”的出現(xiàn)原因及預(yù)防控制
在“手工焊”過程中“錫珠”出現(xiàn)的機(jī)率并不高,常見的是松香飛濺,偶爾會出現(xiàn)“錫珠”的飛濺或者在焊盤的表面殘存有錫渣等;相比較松香的飛濺來講,“錫珠”或錫渣的存在對產(chǎn)品安全性更具潛在危害。
出現(xiàn)錫渣、“錫珠”的主要原因可能是:焊劑在熱源未移開前已完全蒸發(fā),故焊錫流動性極差,沾附烙鐵頭隨烙鐵之抽出而形成尖、柱或短焊情形,或不小心導(dǎo)致焊錫液自烙鐵頭濺離,冷卻后沾附于板面或元件上。還有一種可能是沒有按照先將烙鐵頭放在被焊接部分進(jìn)行預(yù)熱,而是先將焊錫絲燙化,然后再放到被焊位置,因?yàn)檩^大的溫差而造成了焊錫的飛濺,從而形成“錫珠”。
無論是上述哪種原因,更重要的是教導(dǎo)操作人員,把握正確的焊接時(shí)間及位置,適量的添加焊錫并注意及時(shí)、正確地清潔烙鐵頭。在實(shí)際生產(chǎn)中,經(jīng)常對“手工焊”員工進(jìn)行專門的焊接技術(shù)培訓(xùn),并嚴(yán)格編制《手工焊接工藝要求》,對“手工焊”進(jìn)行標(biāo)準(zhǔn)化及可控化的工藝要求。通過長時(shí)間的觀察,目前在“手工焊接作業(yè)”過程中,能夠有效地避免“錫珠”的產(chǎn)生。
結(jié)論:針對“錫珠”問題,我們用了半年多的時(shí)間,和相關(guān)客戶一起,共同做了大量的實(shí)驗(yàn),并對不同的焊接工藝進(jìn)行了細(xì)致的分析。實(shí)踐證明,通過材料選購、工藝控制等,在當(dāng)前的電子焊接制程中,完全有可能杜絕或?qū)?ldquo;錫珠”產(chǎn)生的概率降至更低。
展望未來,將針對焊錫膏配方及生產(chǎn)工藝進(jìn)行一系列的深入再研究,包括“焊錫膏中的溶劑、松香樹脂、活化劑、觸變劑、表面活性劑及其他多種類型添加劑之選用、配伍、配比等,以及焊膏生產(chǎn)工藝所涉溫度、時(shí)間等多個(gè)方面”。希望從產(chǎn)品技術(shù)角度來解決或預(yù)防“錫珠”的產(chǎn)生,以保證在焊接制程中杜絕或更少地出現(xiàn)“錫珠”,從而配合更多客戶達(dá)成焊后“免清洗”工藝。
想要制作優(yōu)質(zhì)的焊錫膏,需要錫粉超微粉碎機(jī),只有原料超微粉碎才能滿足要求。
推薦您閱讀粉體行業(yè)資訊、了解工業(yè)產(chǎn)品技術(shù)、熟悉更多超微粉碎產(chǎn)品百科知識,助您選設(shè)備不求人。
下一篇: 稀土應(yīng)用領(lǐng)域